Molybdenum Disulfide Nanosheet - Friction Lubrication Performance
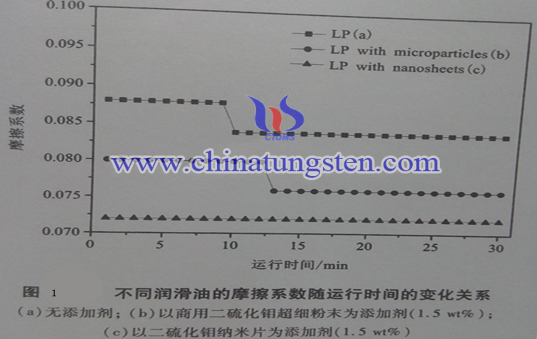
Introduction
Friction mechanism of layered molybdenum disulfide is easy to shear mainly due to van der Waals forces between the layers. When molybdenum disulfide as an additive added to the base oil, the base oil will be adsorbed on the surface of the substrate, molybdenum disulfide particles will also be adsorbed on the substrate. At running time, the particles will be crushed and polished, and then composite lubricating film is formed, then the anti-load level of substrate can be increased and reduced friction and wear. Therefore, the friction coefficient of paraffinic base oils after adding the molybdenum disulphide is markedly reduced (FIG. 1). Because special interface effect, compared to a commercial ultrafine molybdenum disulfide, friction coefficient of molybdenum disulfide nanosheet would be smaller, and has a better operational stability. Molybdenum disulfide nanosheet has a high surface area (75.2 m2 / g), which is 25 times as the ordinary commercial superfine molybdenum disulfide powder, so it can be easy to tightly adsorbed on the substrate surface to form a solid lubricating film, thereby reducing friction and wear.